Introduction
In the realm of operations management, one concept that plays a crucial role in achieving efficiency and success is flow rate. Flow rate, also known as throughput rate, is the measure of how quickly a unit of work or activity moves through a system. It is a key factor in determining the overall performance and productivity of an organization. Understanding and managing flow rate is essential for streamlining processes, optimizing resources, and delivering products or services in a timely manner. This article explores the significance of flow rate in operations management, factors affecting it, strategies for improvement, and tools to optimize flow rate.
What is Flow Rate in Operations Management?
Flow rate in operations management refers to the rate at which work or activities progress through a system. It is a measure of the efficiency with which tasks are completed and resources are utilized. Flow rate is often expressed in terms of units per hour, such as the number of products manufactured, customers served, or transactions processed within a specific time frame. A high flow rate indicates that work is moving swiftly through the system, resulting in increased productivity and customer satisfaction.
What is Flow Time in Operations Management?
Flow time is closely related to flow rate and refers to the total time it takes for a unit of work or activity to move through a system. It encompasses all the stages and processes involved in completing a task, from initiation to completion. Flow time is a critical metric for operations managers as it provides insights into the efficiency and effectiveness of a process. By reducing flow time, organizations can optimize resource allocation, minimize bottlenecks, and improve overall productivity.
Importance of Flow Rate in Operations Management
Efficient flow rate is vital for achieving operational excellence and meeting customer expectations. A high flow rate enables organizations to deliver products or services promptly, reducing lead times and enhancing customer satisfaction. It allows for better resource utilization, minimizing idle time and maximizing throughput. Furthermore, a smooth flow rate ensures that tasks progress without interruptions or delays, reducing the risk of bottlenecks and improving overall efficiency. By focusing on flow rate, organizations can streamline processes, eliminate waste, and ultimately gain a competitive edge in the market.
Factors Affecting Flow Rate in Operations Management
Several factors influence the flow rate in operations management. One key factor is the design of the process itself. A well-designed process with clear steps and minimal complexity tends to have a higher flow rate compared to a process with ambiguous or convoluted steps. The availability and allocation of resources also play a crucial role in determining flow rate. Insufficient resources or poor resource allocation can lead to bottlenecks and hinder the flow of work. Additionally, the skills and capabilities of the workforce impact flow rate. A highly skilled and trained workforce can perform tasks more efficiently, leading to a higher flow rate.
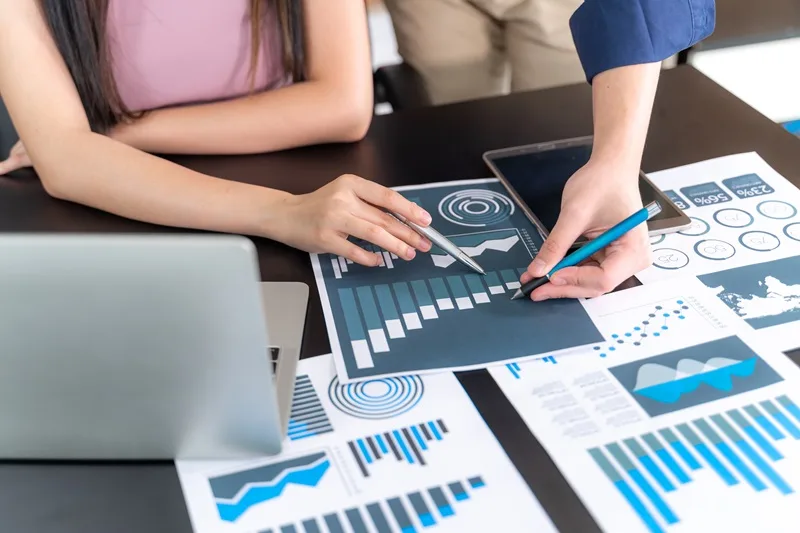
How to Calculate Flow Rate in Operations Management
Calculating flow rate in operations management involves determining the number of units of work that pass through a system within a specific time period. The formula for calculating flow rate is:
Flow Rate = Number of Units / Time
For example, if a manufacturing plant produces 100 units of a product in one hour, the flow rate would be 100 units per hour. It is important to note that flow rate can be calculated for various aspects of operations management, such as production, customer service, or transaction processing. By accurately calculating and tracking flow rate, organizations can measure performance, identify areas for improvement, and make data-driven decisions.
Calculating and Measuring Flow Rate in Operations Management
To accurately calculate and measure flow rate in operations management, organizations need to establish robust measurement systems. This involves collecting relevant data on the number of units or activities completed within a specific time frame. Depending on the nature of the process, data can be collected manually or automatically using sensors or software systems. Once the data is collected, it can be analyzed to calculate flow rate, identify trends, and monitor performance over time. Regular measurement and analysis of flow rate enable organizations to identify bottlenecks, optimize processes, and make informed decisions to enhance efficiency.
Strategies for Improving Flow Rate in Operations Management
Improving flow rate in operations management requires a systematic approach and a focus on continuous improvement. Moreover, here are some strategies to enhance flow rate:
- Process Optimization: Streamline processes by eliminating unnecessary steps, reducing complexity, and improving workflow. Additionally, identify and eliminate bottlenecks to ensure a smooth flow of work.
- Resource Allocation: Ensure efficient allocation of resources to avoid shortages or excesses. Furthermore, optimize resource utilization by matching capacity with demand and implementing lean principles.
- Standardization: Establish standardized procedures and work instructions to ensure consistency and eliminate variations that can hinder flow rate.
- Training and Development: Invest in training programs to enhance the skills and knowledge of the workforce. A well-trained workforce can perform tasks more efficiently, leading to improved flow rate.
- Continuous Monitoring and Improvement: Regularly monitor flow rate and performance metrics to identify areas for improvement. Additionally, implement a culture of continuous improvement to drive ongoing enhancements in flow rate.
Types of Flow Rate in Operations Management
Depending on the specific aspect of operations management under consideration, flow rate can vary. Furthermore, we commonly encounter various types of flow rate. For example, Production Flow Rate measures the rate at which manufacturers or assemblers produce products, indicating the efficiency of the production process and the ability to meet customer demand. Additionally, Customer Service Flow Rate measures how quickly customer service representatives handle inquiries or requests, ensuring timely responses and enhancing customer satisfaction. Transaction Flow Rate gauges the speed at which transactions like order processing, invoicing, or payment processing occur, thus reducing lead times and enhancing operational efficiency. Lastly, Information Flow Rate assesses how quickly information or data moves within an organization, which is crucial for timely decision-making and effective communication.
Tools and Techniques for Optimizing Flow Rate in Operations Management
To optimize flow rate in operations management, organizations can leverage various tools and techniques. Additionally, some commonly used ones include:
- Value Stream Mapping: A visual tool that helps identify waste and inefficiencies in processes. Moreover, it provides a holistic view of the flow of work and enables organizations to make targeted improvements.
- Lean Principles: Lean methodologies, such as Just-in-Time (JIT) and Kanban, focus on eliminating waste, minimizing inventory, and optimizing flow. Furthermore, these principles enhance flow rate by ensuring resources are available when needed.
- Process Automation: Automation technologies, such as robotic process automation (RPA) and workflow management systems, can streamline processes and improve flow rate by reducing manual effort and eliminating errors.
- Capacity Planning: Effective capacity planning ensures that resources are allocated optimally to meet demand. Consequently, by matching capacity with requirements, organizations can maintain a steady flow rate and avoid bottlenecks.
Flow Rate Benchmarks and Industry Standards
Benchmarking flow rate against industry standards and best practices can help organizations gauge their performance and identify areas for improvement. Industry-specific organizations and associations often provide benchmarks and standards that organizations can refer to. By comparing their flow rate with these benchmarks, organizations can identify opportunities to enhance efficiency and stay competitive in the market.
Training and Certification Programs for Understanding and Managing Flow Rate
To gain a deeper understanding of flow rate and its management, professionals can pursue training and certification programs. These programs provide comprehensive knowledge and practical techniques for optimizing flow rate in operations management. They cover topics such as process improvement methodologies, data analysis, and performance measurement. By equipping themselves with the necessary skills and knowledge, professionals can effectively manage flow rate and drive operational excellence.
What is Throughput Rate in Operations Management?
Throughput rate is another term closely related to flow rate in operations management. It refers to the number of units or activities that can be completed within a given time frame. Throughput rate measures the overall capacity of a system to process work. It takes into account factors such as process design, resource availability, and efficiency. By optimizing throughput rate, organizations can maximize their operational capacity and achieve higher flow rates.
What is the Difference Between Cycle Time and Flow Time?
Cycle time and flow time are two metrics used to measure the time taken to complete a unit of work. The main difference between them lies in their scope. Cycle time measures the time it takes to complete one cycle of a specific task or activity, while flow time measures the total time it takes for a unit of work to move through the entire system. Cycle time focuses on individual tasks, while flow time considers the entire process from start to finish. Both metrics are important for understanding and managing flow rate in operations management.
Conclusion: Harnessing the Power of Flow Rate for Operational Excellence
Flow rate is a critical aspect of operations management that significantly impacts an organization’s efficiency and success. By understanding flow rate, organizations can identify bottlenecks, optimize processes, and enhance resource utilization. The strategies, tools, and techniques mentioned in this article provide a roadmap for improving flow rate and achieving operational excellence. By harnessing the power of flow rate, organizations can streamline their operations, deliver value to customers, and gain a competitive advantage in today’s dynamic business environment.
Interested in enhancing your operational efficiency? Read our article Release Management Steps: A Comprehensive Guide to unlock the full potential of your organization.
Leave a Reply