Introduction
In the world of business operations, understanding the concepts of cycle time vs process time is crucial for improving efficiency, productivity, and customer satisfaction. While people often interchange these two terms, they actually represent distinct and crucial metrics that can significantly impact an organization’s performance. This article will delve into the definitions, explanations, and key differences between cycle time and process time, as well as their importance in business operations.
Definition and Explanation of Cycle Time
Cycle time, also known as throughput time, refers to the total elapsed time from the moment a customer places an order or a process is initiated until the final product or service is delivered to the customer. This includes all the steps involved in the production or service delivery process. For instance, order processing, manufacturing, assembly, testing, and shipping. Cycle time is a crucial metric that reflects the overall efficiency and responsiveness of a business’s operations.
Definition and Explanation of Process Time
On the other hand, process time represents the actual time individuals spend actively working on a specific task or step within the overall production or service delivery process. It represents the time spent by employees, machines, or equipment performing a specific operation, such as assembly, testing, or packaging. Process time is a more granular metric that focuses on the individual steps or activities within the larger cycle time.
Are Process Time and Cycle Time the Same?
No, process time and cycle time are not the same. While they are related, they measure different aspects of a business’s operations. Process time focuses on the individual steps or tasks within the overall process. Meanwhile cycle time encompasses the entire end-to-end process. From the customer’s initial request to the final delivery of the product or service.
Importance of Measuring Cycle Time and Process Time
Measuring and analyzing both cycle time vs process time is crucial for businesses. These help to identify areas for improvement, optimize their operations, and enhance customer satisfaction. Cycle time provides a holistic view of the end-to-end process. It allows organizations to identify bottlenecks, streamline workflows, and reduce lead times. Process time, on the other hand, enables businesses to pinpoint specific steps or activities that are causing delays or inefficiencies. It allows them to implement targeted improvements.
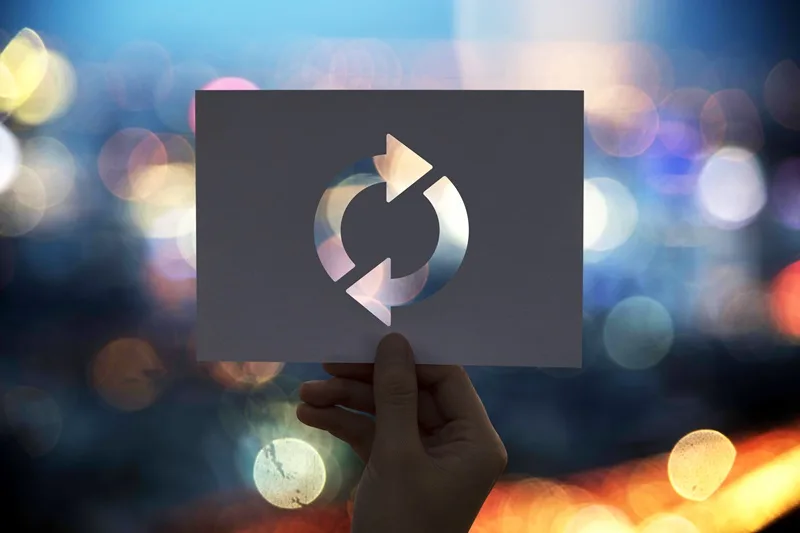
Is Processing Time Greater Than Cycle Time?
In most cases, processing time is less than cycle time. This is because cycle time includes additional time spent on activities. For instance, waiting, transportation, and delays between individual process steps. However, in some instances, processing time can be greater than cycle time, particularly in situations where the process is highly efficient, and the non-value-added time (such as waiting or transportation) is minimized.
How to Calculate Cycle Time and Process Time
To calculate cycle time, businesses typically measure the total elapsed time from the start of the process to the final delivery of the product or service. This includes all the time spent on individual process steps, as well as any waiting, transportation, or other non-value-added activities.
To calculate process time, businesses focus on the time spent actively working on a specific task or activity within the larger production or service delivery process. This can be measured by tracking the time spent by employees, machines, or equipment on a particular step or operation.
What is the Difference Between Cycle Time and Task Time?
The key difference between cycle time and task time is the scope of measurement. Cycle time encompasses the entire end-to-end process. From the customer’s initial request to the final delivery of the product or service. Task time, on the other hand, focuses on the time required to complete a specific, individual task or activity within the larger process.
Their Impact on Productivity and Efficiency
Effectively managing and optimizing both cycle time and process time can have a significant impact on a business’s productivity and efficiency. Reducing cycle time can lead to faster delivery times, improved customer satisfaction, and increased responsiveness to market demands. Optimizing process time can help identify and eliminate waste, streamline workflows, and enhance the overall productivity of the organization.
What is an Example of Lead Time and Cycle Time?
A common example of the relationship between lead time and cycle time can be seen in the manufacturing industry. Lead time refers to the total time from when a customer places an order to when the finished product is delivered. Cycle time, on the other hand, is the time it takes to complete the manufacturing process. From the moment the raw materials are received to the final product being shipped to the customer. While lead time includes the entire end-to-end process, cycle time focuses specifically on the manufacturing operations.
Strategies for Improving Cycle Time and Process Time
Businesses can implement various strategies to improve both cycle time and process time, including:
- Process Optimization: Identifying and eliminating waste, streamlining workflows, and implementing lean manufacturing or service delivery principles.
- Technology Adoption: Leveraging automation, robotics, and digital tools to enhance efficiency and reduce manual, time-consuming tasks.
- Supplier Collaboration: Fostering strong partnerships with suppliers to ensure timely delivery of materials and reduce delays in the supply chain.
- Employee Engagement: Empowering and training employees to identify and address bottlenecks, improve processes, and enhance overall productivity.
- Continuous Improvement: Regularly reviewing and analyzing cycle time and process time data to identify areas for improvement and implement corrective actions.
Conclusion
In conclusion, understanding the distinct concepts of cycle time vs process time is crucial for businesses looking to improve their operations and enhance their competitiveness. By measuring, analyzing, and optimizing these key metrics, organizations can identify areas for improvement, streamline workflows, and deliver superior products and services to their customers. Effective management of cycle time and process time can have a profound impact on a business’s productivity, efficiency, and overall success.
To learn more about how to optimize your business, read our article Platform Engineering: Unlocking Innovation and Scalability
Leave a Reply