Introduction
In the dynamic world of project management, the concept of Kanban has emerged as a powerful tool for streamlining workflows and optimizing efficiency. At the heart of this methodology lies the notion of “lead time”. This is a crucial metric that can make or break the success of a Kanban-driven process. This article delves into the intricacies of lead time in Kanban, exploring its significance, the factors that influence it, and how to leverage it for efficient workflow optimization.
What is Lead Time and Cycle Time in Kanban?
In the context of Kanban, lead time and cycle time are two distinct yet interrelated metrics that provide valuable insights into the performance of a workflow.
Lead Time refers to the total elapsed time from the moment a task or work item is requested until it is completed and delivered to the customer. This encompasses the entire journey, from the initial request to the final delivery.
Cycle Time, on the other hand, measures the time it takes for a task or work item to move through the stages of the Kanban workflow, from the moment it enters the system until it is completed.
Understanding the difference between these two metrics is crucial for effectively managing and optimizing a Kanban-based workflow.
Understanding Lead Time in Kanban
Lead time in Kanban is a critical metric that provides a comprehensive view of the overall efficiency and responsiveness of a workflow. It encompasses the entire duration from the initial request or demand to the final delivery of the completed work item to the customer.
This metric is particularly important because it reflects the customer’s perspective. Moreover, their experience with the organization’s ability to meet their needs in a timely manner. A shorter lead time typically indicates a more efficient and responsive workflow. While a longer lead time may suggest areas for improvement.
Why Lead Time is Important in Workflow Optimization
Lead time stands as a crucial metric in Kanban due to its direct impact on customer experience and the overall workflow’s effectiveness. Several reasons underline the importance of lead time in workflow optimization. Firstly, shorter lead times signify the organization’s ability to swiftly and efficiently respond to customer needs. Thus fostering increased satisfaction and loyalty. Additionally, organizations capable of consistently delivering products or services with shorter lead times often secure a competitive advantage in the market by better meeting customer demands.
Lead time also plays a pivotal role in effective inventory management, aiding organizations in anticipating and planning for future demand. Thereby mitigating the risk of stockouts or excess inventory. Moreover, through analyzing lead time data, organizations can pinpoint bottlenecks, inefficiencies, and areas for improvement within their Kanban workflow. This way it can facilitate process optimization and continuous improvement initiatives. Lastly, lead time data provides valuable insights that inform strategic decision-making processes. For instance, resource allocation, capacity planning, and the introduction of new products or services.
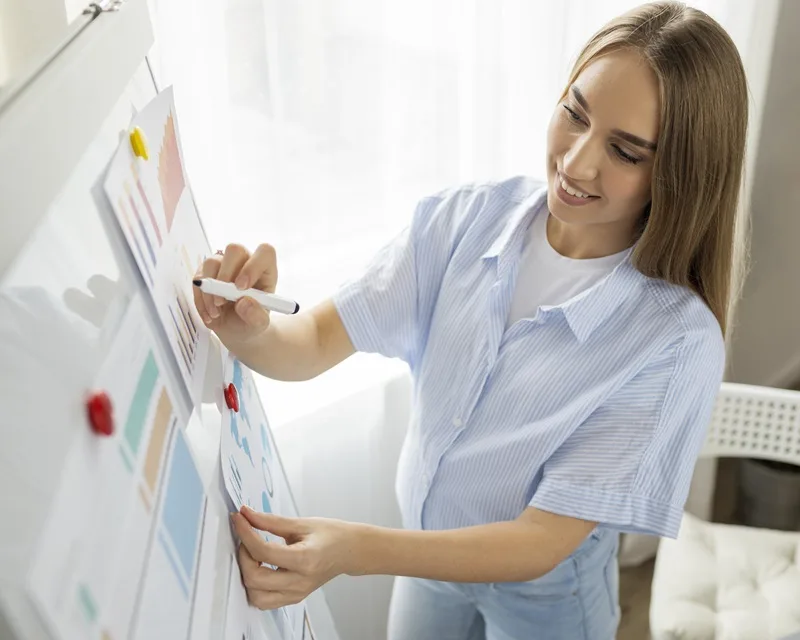
Factors that Impact Lead Time in Kanban
Lead time in Kanban can be influenced by a variety of factors, both internal and external to the organization. It makes it crucial to understand these factors for effective management and improvement. Workflow complexity plays a significant role. The number of steps involved and the interdependencies between tasks can contribute to longer lead times. Additionally, resource availability, including team members, equipment, and materials, can significantly affect task completion and final delivery times. Process inefficiencies such as bottlenecks and delays within the Kanban workflow can also prolong lead times and impact customer satisfaction. External factors like supplier lead times, regulatory changes, or market conditions can further influence lead time. Effective team collaboration and communication are essential for streamlining workflows and reducing lead times. Moreover, the availability and quality of data related to the Kanban workflow. This plays a crucial role in identifying and addressing lead time issues effectively.
How to Calculate Lead Time in Kanban
Calculating lead time in Kanban is a straightforward process that involves tracking the time elapsed from the initial request or demand to the final delivery of the completed work item. Here’s a step-by-step guide on how to calculate lead time:
- Identify the Start and End Points: Determine the specific points in the Kanban workflow where you will measure the lead time. This typically starts with the initial request or demand and ends with the final delivery to the customer.
- Track the Time: Record the timestamp when the work item enters the Kanban workflow and when it is completed and delivered to the customer.
- Calculate the Elapsed Time: Subtract the start timestamp from the end timestamp to determine the total lead time for the work item.
- Aggregate and Analyze: Collect lead time data for multiple work items and analyze the average, median, and distribution of lead times to identify patterns and trends.
By consistently tracking and analyzing lead time data, organizations can gain valuable insights into the performance of their Kanban workflow and identify opportunities for improvement.
How Do I Reduce Lead Time in Kanban?
Reducing lead time in Kanban is an ongoing process that requires a multifaceted approach. Here are some strategies and techniques that can help organizations optimize lead time:
- Streamline the Workflow: Analyze the Kanban workflow and identify opportunities. This will help to simplify or eliminate unnecessary steps, reducing the overall complexity and lead time.
- Improve Resource Allocation: Ensure that team members, equipment, and materials are effectively allocated and utilized to minimize delays and bottlenecks.
- Enhance Process Efficiency: Implement continuous improvement initiatives, such as Lean or Six Sigma. This will help to identify and address process inefficiencies that contribute to longer lead times.
- Enhance Collaboration: Foster effective communication and collaboration among team members. Ensure that information, resources, and decision-making are aligned to support a more efficient workflow.
- Leverage Data and Analytics: Utilize data-driven insights. This is to identify root causes of lead time issues and make informed decisions to address them.
- Implement Kanban Practices: Adhere to Kanban principles, such as work-in-progress (WIP) limits and visual management. Maintain a balanced and efficient workflow.
- Engage Customers: Actively involve customers in the process, gather feedback, and incorporate their input. Align the Kanban workflow with their needs and expectations.
By implementing a combination of these strategies, organizations can systematically reduce lead time and optimize their Kanban-driven workflows.
What is an Example of Lead Time Cycle Time?
To illustrate the difference between lead time and cycle time, let’s consider a simple example:
Imagine a software development team using a Kanban board to manage their workflow. A customer submits a new feature request, and the team initiates the process of developing and delivering the feature.
Lead Time Example:
- The customer submits the feature request on Monday.
- The team starts working on the feature on Tuesday.
- The feature is completed and delivered to the customer on the following Friday.
- The lead time in this example is 5 days, as it took 5 days from the initial request to the final delivery.
Cycle Time Example:
- The team takes 2 days to complete the design and development of the feature.
- The feature then goes through a 1-day testing and quality assurance process.
- Finally, the feature is deployed and delivered to the customer on the 3rd day.
- The cycle time in this example is 3 days, as it took 3 days for the feature to move through the Kanban workflow.
In this scenario, the lead time of 5 days is longer than the cycle time of 3 days. It includes the time between the initial request and the start of the Kanban workflow. As well as any delays or waiting periods outside the direct control of the team.
Understanding the distinction between lead time and cycle time is crucial for effectively managing and optimizing a Kanban-driven workflow.
Some Tools and Software
Effectively managing and optimizing lead time in Kanban requires the use of appropriate tools and software. Here are some popular options for tracking and analyzing lead time:
- Kanban Boards: Digital Kanban boards allow teams to visualize the workflow. They also track the progress of tasks, and collect lead time data.
- Reporting and Analytics Tools: Specialized tools can be used to analyze lead time data, generate reports, and identify trends and patterns.
- Project Management Software: Tools like Microsoft Project often include features for tracking and reporting on lead time and other project metrics.
- Lean or Six Sigma Tools: Software tools can provide advanced analytics and statistical analysis capabilities. They can to help organizations identify and address lead time issues.
- Custom Dashboards: Organizations can also create custom dashboards using tools like Google Data. These help to visualize and monitor lead time data in real-time.
By leveraging these tools and software, teams can effectively track, analyze, and optimize lead time within their Kanban workflows, driving continuous improvement and enhancing overall efficiency.
Conclusion
Lead time is a critical metric in Kanban that provides valuable insights into the overall efficiency and responsiveness of a workflow. By understanding the difference between lead time and cycle time, organizations can gain a comprehensive view of their Kanban processes and identify opportunities for improvement.To learn more about how to optimize your Kanban workflow and reduce lead time, consider enrolling in a Kanban training course or consulting with a Kanban expert. Investing in your team’s Kanban knowledge and skills can help drive continuous improvement and enhance your organization’s competitive edge.
By focusing on lead time and implementing strategies to reduce it, organizations can improve customer satisfaction, gain a competitive advantage, and drive continuous improvement within their Kanban-driven workflows. Leveraging lead time as a key metric in Kanban can be a transformative step towards efficient workflow optimization and long-term success.
To learn more, you can read our article Principles of Agile Methodology: Revolutionize Project Management.
Leave a Reply